The analysis of this paper mainly focuses on four aspects: the structural form selection of the electric wheel, the driving arrangement scheme, the suspension form, and the control of the unspring quality.
This article refers to the address: http://
This article mainly talks about how to design a chassis for small and beautiful electric vehicles. The analysis mainly focuses on four aspects: structural form selection of electric wheel, drive layout scheme, suspension form, and control of non-spring quality.
First, the choice of the structure of the electric wheel
The electric wheels of electric vehicles are classified according to the driving method, and can be divided into two types: deceleration drive and direct drive.
(1) Deceleration-driven electric wheel
The traditional electric wheel originating from the mining vehicle belongs to the deceleration driving type. The electric wheel allows the motor to run at high speed. Generally, the maximum speed of the motor is designed to be between 4000 rpm and 20,000 rpm, in order to obtain a higher specific power. A common inner rotor high speed motor is usually used. The speed reducer is arranged between the motor and the wheel to reduce and increase the torque, thereby ensuring that the electric vehicle can obtain a sufficiently large torque at a low speed.
The advantages of the decelerating drive type electric wheel motor are high speed, high specific power, light weight, high efficiency, low noise and low cost. However, because the motor speed is large, the speed reducer must be used to reduce the speed to obtain a large turn. Moment, so the quality of the entire electric wheel as an unsprung mass will be much heavier than that of a conventional internal combustion engine.
(2) Direct drive type electric wheel
This type of electric wheel mostly uses an outer rotor motor, and the outer rotor is directly mounted on the rim of the wheel to drive the wheel to rotate. Electric vehicles require a large torque at the start, so the motor installed in the direct drive type electric wheel must be able to provide a large torque at a low speed. In order to make the car have better power, the motor must also have Wide range of torque and speed adjustments and guaranteed high efficiency in this range.
The outer rotor motor used in the direct drive type electric wheel has a simple structure, small axial dimension, high specific power, can control torque over a wide speed range, and has a fast response speed, and has high efficiency because there is no reducer. Compared with the decelerating drive type electric wheel, it is easier to realize the wheel anti-lock braking system, which is easier to implement the wire control technology and better improve the steering stability of the electric vehicle; but the efficiency is not too high during acceleration, and the noise Very big.
Li Xiang’s “small and beautiful†total motor power should be less than 15kw, the maximum speed is expected to be around 100KM/h, and the speed is not high. It is expected to use a direct-drive electric wheel. The structure is similar to the following:
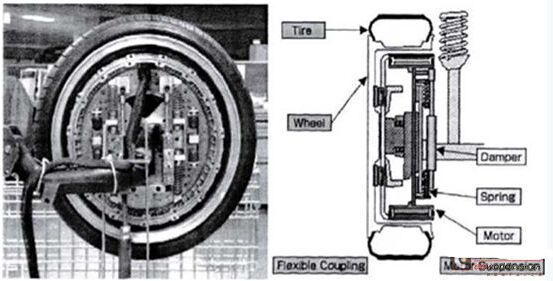
Second, the wheel motor selection
The common forms of hub motors are as follows: brushless DC motors, switched reluctance motors, induction motors, disk permanent magnet motors, axial field motors, Weh's transverse magnetic field permanent magnet motors, permanent magnet synchronous motors and other forms of motors. The hub motor is battery powered, and the compact design, high efficiency and high reliability are the most basic design requirements. In addition, indicators such as simple control, good dynamic response, and small inrush current are also expected to be guaranteed. Similar to the "small and beautiful" products, the power of a single motor is small, taking into account the maturity of the technology, it is expected that the design selection may give priority to the following points:
1. Permanent magnet motor may be the first choice and use high performance NdFeB permanent magnet material. In this way, it is possible to simplify the motor structure to the utmost, reduce the volume of the motor, and design a high power density, high efficiency motor.
2. Use an axial magnetic field structure. This is not only the actual need of the flat shape of such a motor (large axial cross-sectional area, small circumferential surface area), but also a scientific choice for the long axis of the axial magnetic field motor and the short-circuit avoidance of the radial magnetic field motor. The space utilization of the motor will be higher, the structure will be more compact, the material will be more economical, and the performance will be superior.
3. Choose a larger motor outer diameter (meaning a larger tire diameter, which is actually more advantageous for the shape). The hub motor is not as small as possible. When the torque is constant, the smaller the wheel diameter, the greater the shearing force. As a result, the fatigue strength of the component is reduced and the possibility of damage is increased. For electric vehicles, this means that the hub is more susceptible to damage, life is reduced, and reliability is reduced. In addition, when the motor loss is constant, the smaller the volume, the higher the temperature, and since the heat dissipation area at this time is relatively small, the temperature rise is inevitably higher. It can be seen that the small outer diameter motor is disadvantageous for improving performance and operational reliability.
Third, the drive unit layout program
Wheel drive unit can be divided into four-wheel drive mode, 2 conventional drive wheel + 2 wheel drive wheel, 2 front wheel short half-axis plus wheel motor + 2 rear wheel drive and 4 short drive according to the drive form. Half shaft plus wheel Yi motor form. For example, the following figure is a structural diagram of an electric vehicle using a 2 front wheel short half shaft plus hub motor + 2 rear wheel wheel side drive.
As can be seen from the comparison of the following figures, in the four drive forms a, b, c and d, the structure of the electric wheel drive is the simplest and most compact, and the space occupied is the least, which not only provides a larger By taking the space, the floor of the car is also lowered, so that the center of gravity of the car is greatly reduced, and the stability of the car is improved.
Because of the "small and beautiful" vehicle, the body size is small and the layout space is limited. It is expected that the four-wheel wheel-driven structure will be adopted, as shown below:
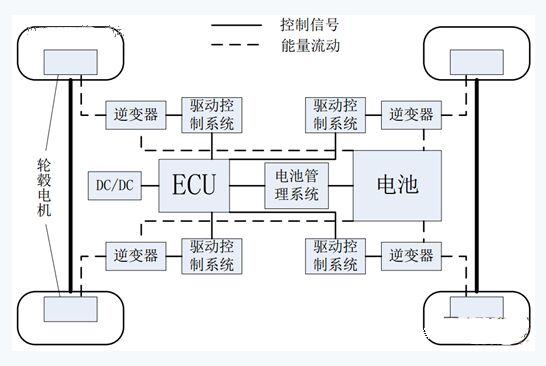
Fourth, the choice of front / rear suspension program
Compared with the independent suspension, the non-independent suspension has a relatively high quality and is not suitable for the wheel-side driving electric vehicle suspension system. Common independent suspensions used in conventional vehicles include: single wishbone type, single trailing arm type, single inclined arm type, longitudinal arm torsion beam type, MacPherson type, double wishbone type, and multi-rod type.
Different suspension systems have different structural complexity, so there is a difference in the amount of materials required. At the same time, due to the different connection modes of the suspension, the components in the suspension have different proportions between the unsprung mass and the sprung mass, and the torsion bar The double wishbone suspension, in which the spring constitutes the elastic element, has considerable advantages in terms of suspension performance and weight reduction, and is therefore suitable for a suspension system for driving an electric vehicle on a wheel side. This type of suspension system is widely used in traditional vehicles, such as IVECO series front independent suspension assembly, JAC Ruifeng commercial vehicle series front independent suspension assembly, etc., all adopting unequal length double wishbone torsion bar spring suspension system. . Due to the small size of the car body, it is expected that a single trailing arm type rear suspension will be adopted, which does not occupy a high space, and can provide a maximum space for the battery pack to be placed, which is advantageous for improving the driving range of the electric vehicle.
Considering the materials used in the suspension system and key components, the suspension system is expected to use aluminum alloy, titanium alloy, magnesium alloy, composite materials (such as glass fiber reinforced resin composite materials, carbon fiber reinforced resin materials, color plastics), etc. The aluminum alloy suspension or aluminum alloy rim applied to the automobile can reduce the unsprung mass of the whole vehicle. The design of the wheel drive system will also adopt lightweight materials. For example, the outer casing of the hub motor and the rim are made of aluminum alloy material, which reduces the unsprung mass of the whole vehicle as a whole.
Aluminium Parts For Automotive
Aluminium Parts For Automotive,Aluminium Automotive Parts,Automotive Aluminium Profile,Automotive Aluminium Parts
KAM KIU ALUMINIUM GROUP , https://www.kamkiualuminium.com