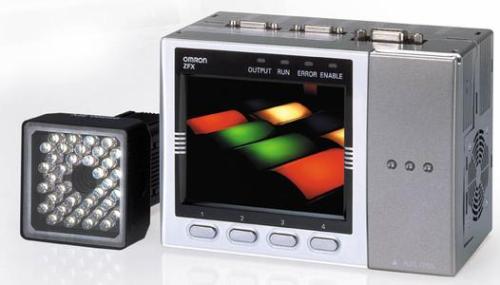
2. The general structure of the control of the overall control can refer to the following figure, where I will briefly explain the overall control content. This is a case of position correction for FPD glass substrates. As an application of this control, it can also be applied to adhesion of an FPD glass substrate, correction of a substrate position of an electric product, positional correction of an electronic component during processing, and the like. In general, the mechanical axis is constituted by the drive axes of the X-axis, Y-axis, and θ-axis, and a visual sensor for determining the load on the workbench is provided to perform data calculation between the two, and the servo control for driving the mechanical table is performed. Form the entire system.
1 For the load to be machined, it is necessary to print a mark in order for the vision sensor to make the discrimination. To achieve better accuracy, you need more than 2 markers.
2 The load is placed on the mechanical table for processing.
(2) The visual sensor discriminates the mark printed on the above-mentioned load, and compares it with the previously set (memorized) position, and then calculates the error with high accuracy.
3 The error calculated by the vision sensor is converted by the PLC into the movement amount of the machine, and the position of the correction error is set and implemented.
3. In this control, the visual sensor is one of the most important points for improving the accuracy of the visual sensor. If the visual sensor can't discriminate the position with good precision, the improvement precision in this control can't be achieved either. Our vision sensors, from experience and technology, can achieve the following functions for improving the accuracy of discrimination.
â—High precision Search
The most similar portion to the memorized marker data is discriminated, and highly accurate position data calculation is performed.
When printing a mark on a load, it is more difficult to print the same mark each time. Printing defects or poor printing may occur. However, if this function is used, it is possible to determine the accuracy even if the label printed on the actual load differs from the registered label.
â—ECM (Edgecodemodel) Search
The edge of the memorized label (not the entire label, only one circle around) is registered as a typical image, and the most similar portion is identified from the image data actually received. When the glasses overlap each other, there is an example where the labels to be determined overlap with each other. In this function, because of the typical registration in the form of tag edge data, even if a tag overlaps, it is possible to discriminate what shape one circle is around, thereby achieving high-precision judgment.
4. The position information that is identified in the calibration vision sensor is used as the pixel data inside the vision sensor to discriminate. However, if the relationship between the pixel data and the actual movement distance of the table is not clear, the positional correction of the load cannot be achieved.
The so-called calibration is to clarify the relationship between the position recognized by the vision sensor and the position accuracy of the actual table, and remember it.
We put this calibration function on the vision sensor, PLC, servo control program, and realize it in automatic control mode.
When the load's reference position is registered, the following actions are performed and the calibration is completed.
When the actual load is moved, the following errors can be corrected by calculating the visual sensor position information at that time.
â— Camera installation error: When the installation of the camera is not completely vertical, the error can be corrected.
â— Mechanical table movement error: It corrects the error of the amount of movement due to machining accuracy.
â— Mechanical bench setup error: Correction of the error in the construction of the drive shaft of the mechanical table.
5. Motion Compensation Calculation Finally, it is necessary to move the table using the position correction amount determined by the visual sensor.
It should be noted that the organization of the workbench will vary according to the site case.
In recent years, the size of glass in the FPD industry has become larger, and a UVW workbench has been added.
The UVW table has a feature that the maximum movement stroke is small and the rotation angle accuracy is high.
When the size of the load (the length between the marks) becomes large, the offset caused by the angle error also becomes large, which is effective in suppressing such an error.
In addition, the drive shaft of such a table is on a single plane, and compared with the laminar overlap of the previous XYθ drive shaft, it is a lighter and thinner mechanism, and has a lightweight feature.
6. The final realization of precision In the actual case, this type of vision sensor was used for high-precision positioning control, and the requirement for positioning accuracy of 10 μm or less was achieved.
The constituent machine of this case is as follows.
â— Vision Sensor: F210-C10
â— Camera used: F160-SLC20 (view angle 20mm)
â— PLC: CJ1H-CPU66H
â— Serial Communication Unit: CJ1W-SCU21-V1
â— Positioning Control Unit: CJ1W-NC433
â— Servo driver: R7D-APA3L (SmartStep)
ABB Robotics DCS series offers Backplane Connectors, Analog Input Output Modules, Converter Boards and Robot Computers.
ABB Safety Board,ABB Robots I/O Board,ABB Robot Rectifier Unit,Robot CPU Module
Xiamen The Anaswers Trade Co,.LTD , https://www.answersplc.com